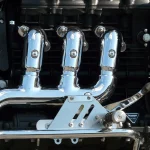
Exhaust Headers
December 19, 2024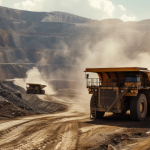
Mining Trucks Exhaust Systems: The Crucial Role of Mufflers
March 3, 2025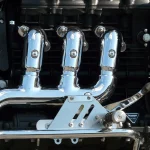
Exhaust Headers
December 19, 2024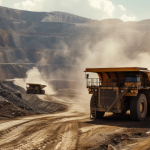
Mining Trucks Exhaust Systems: The Crucial Role of Mufflers
March 3, 2025Automotive sensors are critical components in modern vehicles, providing essential data for various systems to ensure safety, efficiency, and performance. These sensors monitor and report on various parameters, such as pressure, position, and more, enabling advanced functionalities like adaptive cruise control, self-driving, and engine management. These sensors' product design and development are crucial to their effectiveness and reliability.
In this post, we will explore some mechanical design aspects when designing an automotive sensor, focusing on some considerations and processes involved in creating reliable and efficient sensors for automotive applications.
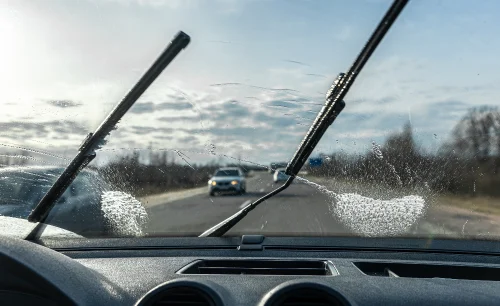
Examples of Automotive Sensors
Each type of sensor has a specific role in the vehicle's operation. For example, temperature sensors help manage engine cooling, while pressure sensors ensure proper tire inflation pressure.
Categorization: Automotive sensors can be categorized into several types based on their functionality:
- Acoustic Sensors: Detect and analyze sound waves within the vehicle. For example, acoustic sensors can be used for noise, vibration, and harshness (NVH) analysis to improve cabin comfort by identifying and mitigating unwanted noises. They are also used in parking assistance systems to detect obstacles.
- Temperature Sensors: Measure the temperature of various vehicle components.
- Pressure Sensors: Monitor the pressure of fluids and gases within the vehicle.
- Position Sensors: Detect the position of various parts, such as the throttle or camshaft.
- Speed Sensors: Measure the rotational speed of wheels or the engine.
- Oxygen Sensors: Monitor the oxygen levels in the exhaust gases to optimize fuel combustion.
Mechanical Design Considerations
Durability and Reliability:
Designing sensors that can withstand harsh automotive environments is crucial. These sensors must endure extreme temperatures, vibrations, moisture, and exposure to chemicals without compromising their performance.
- Temperature Limits: Automotive sensors must operate reliably within a wide temperature range. For example, engine temperature sensors typically function from -40°C to +130°C, while exhaust gas temperature sensors can handle temperatures up to +1000°C. These limits are often guided by standards such as ISO 16750-4, which outlines environmental conditions and testing for electrical and electronic equipment in road vehicles.
- Vibration Limits: Sensors must also withstand significant vibrations. According to ISO 16750-3, automotive sensors should be tested across a frequency range of 10 Hz to 2000 Hz with varying levels of acceleration. This ensures they can endure the vibrations experienced during vehicle operation and transport.
- Moisture Limits: Moisture resistance is essential to prevent sensor failure due to water ingress. Automotive sensors are often tested to meet IP67 or IP69K standards, which ensure protection against dust and water immersion up to 1 meter for 30 minutes (IP67) and high-pressure, high-temperature water jets (IP69K).
- Chemical Corrosion Limits: Sensors must resist corrosion from exposure to various chemicals, such as road salts and engine fluids. Standards like ISO 22858 provide guidelines for monitoring atmospheric corrosion using electrochemical measurements. These sensors are designed to withstand exposure to corrosive environments, ensuring long-term reliability.
By adhering to these standards and limits, automotive sensors can maintain their performance and reliability in the demanding conditions of automotive applications.
Material Selection:
When it comes to the selection of materials, automakers prefer certain types of materials according to the sensor’s functionality, loads, and location in the vehicle. The most commonly used materials include:
- Metals: For structural components due to their strength and durability.
- Plastics: For housings and connectors, offering lightweight and corrosion resistance.
- Ceramics: For components that require high-temperature stability and electrical insulation.
Here's a table summarizing the mechanical properties of commonly used materials in each category:
Category |
Material |
Density (g/cm³) |
Tensile Strength (MPa) |
Young's Modulus (GPa) |
Thermal Conductivity (W/m·K) |
Operating Temperature (°C) |
Metals |
Aluminum Alloy |
2.7 |
200-600 |
70-80 |
150-235 |
-40 to 150 |
Stainless Steel |
7.8 |
500-1000 |
190-210 |
15-25 |
-40 to 800 |
|
Copper |
8.9 |
210-250 |
110-130 |
390-400 |
-40 to 200 |
|
Plastics |
Polypropylene (PP) |
0.9 |
30-40 |
1.5-2.0 |
0.1-0.22 |
-20 to 120 |
Polyamide (Nylon) |
1.1-1.2 |
70-100 |
2.5-3.5 |
0.25-0.3 |
-40 to 120 |
|
Polycarbonate (PC) |
1.2 |
60-70 |
2.0-2.4 |
0.19-0.22 |
-40 to 135 |
|
Ceramics |
Alumina (Al₂O₃) |
3.9 |
300-600 |
300-400 |
20-30 |
-40 to 1600 |
Zirconia (ZrO₂) |
5.6 |
900-1200 |
200-220 |
2.5-3.0 |
-40 to 2400 |
|
Silicon Carbide |
3.2 |
400-600 |
410-450 |
120-200 |
-40 to 1600 |
These materials are selected based on their mechanical properties, which ensure the sensors can perform reliably under the demanding conditions of automotive applications.
Size and Weight:
Minimizing the size and weight of sensors is essential to reduce the overall vehicle weight and improve fuel efficiency. However, this must be balanced with the need to maintain sensor performance and durability.
Automotive Product Development Process (PDP)
Agile Iterative Design:
Incorporating the agile iterative design concept makes the design process more flexible and adaptive. This approach involves breaking down the design process into smaller, manageable iterations or sprints. Each iteration includes planning, designing, prototyping, testing, and reviewing. Feedback from each iteration is used to refine and improve the design continuously. This iterative process helps identify and address issues early, leading to a more robust and reliable sensor.
Concept Development >> Design and Engineering >> Prototyping and Testing >> Production Planning >> Manufacturing
-
Concept Development: This initial phase involves identifying market needs, generating ideas, and defining the product concept. It includes feasibility studies, market analysis, and initial design sketches. The primary focus should be on functionality, ensuring the sensor meets its intended purpose. If the sensor is exposed, industrial designers should also consider:
- Functionality
- Ergonomics
- Aesthetic appeal
- Marketability
-
Design and Engineering: In this stage, detailed design work is carried out using tools like CAD (Computer-Aided Design) software. Engineers focus on creating detailed 3D models, selecting materials, and ensuring the design meets all functional and regulatory requirements.
-
Prototyping and Testing: Prototypes are built and tested to validate the design. This phase includes rigorous testing for performance, durability, safety, and compliance with standards. Iterative testing and refinement are crucial to address any issues that arise.
-
Production Planning: This stage involves planning the manufacturing process, including tooling, production line setup, and supply chain logistics. It ensures that the product can be produced efficiently and at scale.
-
Manufacturing: The product is manufactured according to the planned processes. Quality control measures are implemented to ensure consistency and adherence to specifications.
-
Launch and Post-Launch: The product is launched into the market. Post-launch activities include monitoring product performance, gathering customer feedback, and making any necessary adjustments or improvements.
Integration with the Vehicle
Mounting and Installation:
Automotive electronics use common automotive-grade wires, sockets, and plugs. Depending on the type of communication needed, ready-made sockets from suppliers like Rosenberger can be used. A hermetically sealed connection should be considered to maintain the sensor's IP/NEMA rating. There are two options to consider:
- A built-in plug/socket in the sensor’s enclosure.
- A built-in wire with a plug/socket at the free end.
The installation location should be predefined, and sufficient testing should be performed on the sensor’s performance with the vehicle's vibration and harshness.
Automotive Sensors Connectors (Plugs and Sockets)
Below is a list of top connector vendors:
- TE Connectivity
- Yazaki
- Aptiv (Delphi)
- JAE
- J.S.T
- Sumitomo
- Rosenberger
- AVX
- Amphenol
- Molex
- ACDelco
Automotive Cables
The following properties are important to know when selecting your cable:
- Data transfer rate
- Shielding material
- Core material
- Core type (fiber or solid)
- Clock frequency
- Insulation material
- Impedance
- Maximum diameter of the single wire
- Nominal diameter of the conductor
- Number of strands
- Electrical resistance at 20 °C max. (ohm/km)
- Temperature range
- Capacity [max. pF/m]
- Jacket material
- Weight (kg/m)
- Twisted pair or Multiconductor
- Strand coating
- Flammability
- Cable Resistance RDC
Below is another list of top automotive cable suppliers:
- BorgWarner, Inc.
- Furukawa Electric Co. Ltd.
- Lear Corporation
- LEONI AG
- Nexans Autoelectric GmbH
- Motherson Group
- Sumitomo Electric Industries, Ltd.
- AmWINS Group Inc.
- YAZAKI Corporation
- YURA Corporation
Automotive Compliance
Compliance with industry standards and regulations is crucial for the success of automotive sensors. Adhering to directives such as the Electromagnetic Compatibility (EMC) Directive and the Low Voltage Directive (LVD) ensures that the sensors do not interfere with other electronic devices and provide a high level of safety for users. Meeting these standards not only guarantees the product's reliability and safety but also enhances its marketability by building trust with consumers and regulatory bodies. Additionally, obtaining relevant certifications like AEC-Q100, ISO/TS 16949, and ISO 26262 demonstrates a commitment to quality and safety, which can significantly influence the product's acceptance in the market. Compliance with organizational standards such as IATF 16949 and ISO 9001 further supports the manufacturing of safe and reliable products, ultimately determining the product's success and longevity in the competitive automotive industry.
Electromagnetic Compatibility (EMC) Directive: Ensures that the product does not affect nearby electronics by emitting electromagnetic waves. For example, old cell phones affect radios and TVs.
The Low Voltage Directive (LVD): Ensures that electrical equipment within certain voltage limits provides a high level of protection for European citizens. The LVD covers health and safety risks on electrical equipment operating with an input or output voltage of between:
- 50 and 1000 V for alternating current
- 75 and 1500 V for direct current Link.
Relevant Certificates |
Organizational Standards |
|
|
Testing
Testing is critical in developing automotive sensors, ensuring they meet all necessary performance, safety, and reliability standards. Comprehensive testing helps identify potential issues early, reducing the risk of failures in real-world applications. By adhering to relevant standards, manufacturers can ensure their sensors are robust, reliable, and compliant with industry regulations, ultimately determining the product's success in the market.
Here's a table summarizing the testing values that could apply to most sensors, along with examples and relevant standards:
Category |
Property |
Example |
Relevant Standard |
Technical |
Min. range |
Minimum detectable pressure |
ISO 26262 |
Max. range |
Maximum temperature measurement |
ISO 16750-4 |
|
Detection zone |
Area covered by a proximity sensor |
ISO 17387 |
|
Safety level (ASIL) |
Automotive Safety Integrity Level |
ISO 26262 |
|
Dynamic |
Sensitivity |
Sensitivity of an accelerometer |
SAE J211/1 |
Frequency Response |
Frequency range of a vibration sensor |
ISO 5348 |
|
Dynamic Range |
Range of measurable speeds for a speed sensor |
ISO 11452-2 |
|
Phase Match |
Phase accuracy in multi-sensor systems |
ISO 6487 |
|
Resonance Frequency |
Resonance frequency of a pressure sensor |
ISO 5348 |
|
Temperature Response |
Response time to temperature changes |
ISO 16750-4 |
|
Electrical |
Input Voltage |
Voltage range for sensor operation |
ISO 16750-2 |
Current |
Current consumption of the sensor |
ISO 7637-2 |
|
Electrical Noise |
Noise level in sensor output |
ISO 11452-2 |
|
Output Impedance |
Impedance of the sensor output |
ISO 11452-2 |
|
Bias output voltage |
Nominal bias voltage |
ISO 16750-2 |
|
Grounding |
Grounding requirements for sensor installation |
ISO 11452-2 |
|
Environmental |
Operating Temperature |
Temperature range for sensor operation |
ISO 16750-4 |
Influence of Humidity |
Sensor performance under high humidity |
ISO 16750-4 |
|
Storage Temperature |
Temperature range for sensor storage |
ISO 16750-4 |
|
IP/NEMA Label |
Ingress protection rating |
IEC 60529 |
|
Vibration Sensitivity |
Sensitivity to mechanical vibrations |
ISO 16750-3 |
|
Magnetic Field Sensitivity |
Sensitivity to magnetic fields |
ISO 11452-8 |
|
Physical |
Weight |
Weight of the sensor |
ISO 16750-4 |
Case Material |
Material used for sensor housing |
ISO 16750-4 |
|
Mounting |
Mounting method and stability |
ISO 16750-3 |
|
Output Connector |
Type of connector used for sensor output |
ISO 15031-6 |
|
Car connectivity |
Compatibility with vehicle communication systems |
ISO 14229 |
|
Car communication |
Communication protocols used by the sensor |
ISO 14229 |
This table provides a comprehensive overview of the various testing parameters, examples, and relevant standards that ensure the reliability and performance of automotive sensors.
Future Trends
Advancements in Sensor Technology: The field of automotive sensors is rapidly evolving, with emerging trends and technologies enhancing their capabilities. One notable advancement is the integration of AI and machine learning for predictive maintenance, which allows sensors to anticipate and diagnose potential issues before they become critical. Additionally, developing more compact and energy-efficient sensors enables their use in a wider range of applications, contributing to overall vehicle efficiency.
Example—AutoHears: AutoHears is a cutting-edge example of future acoustic sensor technology. This innovative system allows vehicles to "hear" their surroundings, detecting, classifying, and localizing sounds such as sirens, horns, and even natural disasters like rockslides. AutoHears enhances safety by enabling vehicles to respond to auditory cues beyond traditional visual sensors' reach, making it particularly valuable for autonomous driving systems.
References
- SSZT099 Technical article | TI.com
- Vibration Testing Standards and Requirements for Automotive Manufacturers
- Essential Temperature Sensors in Automobiles and Their Roles
- AutoHears | Your Ears on the road
- AVs Need to See and Hear What’s Coming - EE Times Europe
-
Proposal of framework to managing the automotive product development process
Contact Us
We'd love to hear from you! Whether you have questions, need a consultation, or want to discuss a project, feel free to reach out.
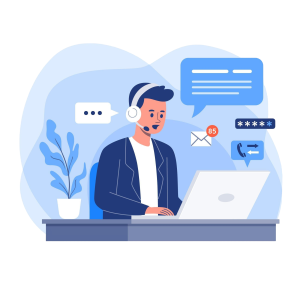